Los nuevos perfiles profesionales en el marco de la Industria 4.0
En este artículo se analizan los motivos que limitan la adopción de las nuevas tecnologías y frenan el proceso de transformación digital de las empresas del tejido industrial. Más allá de los aspectos técnicos o económicos, el origen de estos frenos en el marco de la Industria 4.0 radica en la falta de transversalidad de los perfiles profesionales existentes actualmente. En vista de esto, en el artículo también se analiza el impacto laboral y los nuevos perfiles profesionales que serán necesarios para hacer frente al proceso de transformación digital, así como el rol que tendrán los expertos, los grupos de trabajo y las herramientas de diagnosis en este proceso.
This article analyses the reasons that limit the adoption of new technologies and slow down the digital transformation process of companies in the industrial sector. Beyond technical or economic aspects, the origin of the slowdown lies in the lack of transversality of existing professional profiles in the context of Industry 4.0. In view of this, the article also analyses the labour impact and the new professional profiles that will be necessary to deal with the digital transformation process, as well as the role that will be played by experts, working groups and diagnostic tools in this process.
La transformación digital [1] es el proceso de adopción de las tecnologías digitales, tanto en el plano individual como colectivo, que está provocando cambios sustanciales en los distintos ámbitos donde se llevan a cabo actividades socioeconómicas. En 2015, la consultoría Boston Consulting Group [2] definió las tecnologías que son la base de este proceso de transformación digital, entre las que destacan: robótica colaborativa, simulación, Internet de las cosas, ciberseguridad, computación en la nube, impresión aditiva, realidad aumentada, analítica de datos e inteligencia artificial.
En el sector industrial, el proceso de transformación digital se conoce con el nombre de Industria 4.0 [3] y hace referencia al impacto que tiene la aplicación de estas tecnologías tanto en el diseño de los productos como en la mejora de los procesos de fabricación. Por ejemplo, la combinación de Internet de las cosas, computación en la nube e inteligencia artificial habilita el despliegue de soluciones de mantenimiento predictivo, que permiten monitorizar el funcionamiento de las máquinas de manera continua y anticiparse a un mal funcionamiento, y así evitar paradas de línea y determinar la raíz del problema [4].
Pero las mejoras pueden ir más allá de ser optimizaciones de los sistemas ya existentes. Por ejemplo, la combinación de estas tecnologías permite construir sistemas productivos con unos altos niveles de flexibilidad y de automatización, de manera que se puede producir con medidas de lote muy pequeñas, llegando al límite con el lote de medida uno [3]. Así pues, el proceso de transformación digital en el ámbito de la industria dará lugar a productos más personalizados, de mejor calidad y producidos a un coste más bajo, pero también tendrá el potencial de revolucionar los modelos de negocio de las empresas tradicionales, pasando de modelos basados en la venta de productos a modelos basados en la oferta de servicios.
Teniendo en cuenta el potencial transformador de estas tecnologías, pero también su complejidad y coste, se espera que el proceso de adopción de las mismas por parte de la industria siga el modelo de difusión de la innovación propuesto por Rogers [5]. En este modelo, las empresas se pueden clasificar siguiendo una curva normal como innovadoras (2,5%), seguidoras iniciales (13,5%), mayoría precoz (34%), mayoría tardía (34%) y atrasadas (16%)1. Si sumamos el número de usuarios que han adoptado una tecnología a medida que avanza el tiempo (integral de la curva de difusión a lo largo del tiempo) obtenemos la curva agregada de difusión, que adquiere forma de S [5], y en la que se distinguen tres tramos de adopción: un primer tramo de crecimiento lento, un tramo de fuerte aceleración con pendiente máxima alrededor del punto medio y, finalmente, un tramo de ralentización que tiende a pendiente cero, tal y como se muestra en la Figura 1.
Figura 1. Curvas de Rogers de adopción y de adopción agregada de las tecnologías
Así pues, las empresas que adopten estas nuevas tecnologías a tiempo podrán capturar el valor añadido que aportan (es decir, nuevos productos, aumento de calidad, reducción de costes, aumento de la eficiencia, nuevos modelos de negocio, etc.), consiguiendo así una parte más grande de la cuota de mercado actual o abriendo nuevos mercados todavía inexistentes. Por el contrario, las empresas que las adopten tarde o que no las adopten correrán el riesgo de ser superadas por sus competidores en el ámbito global y tenderán a desaparecer.
A la vista de esta realidad, en el artículo nos proponemos llevar a cabo una visión sobre el proceso de adopción de la tecnología en el marco de la Industria 4.0, y del impacto que ello tiene en los nuevos perfiles profesionales que son necesarios para facilitar la adopción de estas tecnologías.
El resto del artículo está organizado como sigue a continuación: en la sección 2 se presentan los modelos de adopción y el estado actual de la adopción tecnológica en el marco de la Industria 4.0; en la sección 3 se analiza el impacto laboral de la Industria 4.0 y los nuevos perfiles profesionales que se derivan del proceso de transformación digital; en la sección 4 se analiza la figura de los expertos, los grupos de trabajo y las herramientas de diagnóstico para impulsar y evaluar la adopción de las tecnologías digitales en el marco de la Industria 4.0; finalmente, en la sección 5 se presentan las conclusiones del artículo.
En esta sección presentamos un modelo que explica las palancas y los frenos que inciden en el proceso de adopción de la tecnología en el marco de la Industria 4.0, así como una revisión del nivel actual de adopción.
En el año 2015, la consultoría McKinsey publicó un informe [6] donde presentaba un modelo que pretendía explicar el proceso de adopción tecnológica en el marco de la Industria 4.0 mediante drivers (impulsores) y levers (palancas)2. En primer lugar, los drivers (impulsores) son los ámbitos de interés de una empresa (beneficio económico, estructura organizativa o de procesos, y de visión y valores) susceptibles de ser transformados; por ejemplo, la gestión de los recursos y de los procesos productivos, la utilización de los activos, la gestión del trabajo, la gestión del inventario, la garantía de la calidad, el equilibrio entre la oferta y la demanda, los tiempos en mercado y los servicios posventa, entre otros. En segundo lugar, los levers (palancas) son aquellos ámbitos de actividad (procesos) susceptibles de ser modificados mediante la aplicación de una o más tecnologías, y que dan valor (por ejemplo, reducción de costes o de tiempos, aumento de la productividad, etc.) a los drivers a los que están asociados.
En general, estas palancas ya existen en la actualidad, de manera que la aplicación de las nuevas tecnologías les da más potencial transformador. Por ejemplo, una de las palancas de la Industria 4.0 sería el mantenimiento predictivo, que corresponde al ejemplo mencionado en la introducción. Si bien esta palanca ya existía, ha sido la combinación de las tecnologías Internet de las cosas, computación en la nube e inteligencia artificial lo que ha permitido darle un gran impulso y hacer que tenga impacto en el driver utilización de los activos. Ello ha sido posible gracias a la comoditificación de la oferta tecnológica que ofrece productos y servicios de tipo genérico, y a unos precios asequibles. De manera similar, la palanca de ingeniería concurrente ha sido empoderada gracias a la combinación de la fabricación aditiva y de la simulación y a la mejora del driver tiempo de mercado.
Así pues, la utilización conjunta de las tecnologías propuestas por Boston Consulting Group y el modelo de drivers y levers de McKinsey permite determinar las relaciones entre las diferentes tecnologías y el beneficio que aportan a las empresas industriales, de manera que explica la motivación que lleva a las organizaciones a adoptarlas para mejorar sus productos, procesos productivos y procesos de gestión. En cambio, estos modelos no especifican cuál es el proceso que deben seguir las empresas industriales para adoptar estas tecnologías y obtener los beneficios esperados, según los informes de estas consultorías. Este es un punto crítico en la adopción de la Industria 4.0 en el tejido industrial, puesto que, como hemos dicho antes, es la combinación de diferentes tecnologías la que permite activar ciertas palancas para dar valor a un impulsor específico.
Siguiendo con el símil mecánico, en contraposición a las palancas, que tienen una vocación impulsora, también se han identificado frenos a la adopción de las tecnologías habilitadoras de la Industria 4.0. Por ejemplo, varios estudios realizados por PricewaterhouseCoopers [8], KPMG [9], la Comisión Europea [10], la VDI y la ASME [11] indican que el freno más importante para la implementación efectiva de la Industria 4.0 es la falta de perfiles profesionales adecuados, y que esta es consecuencia directa de la carencia de transversalidad de los perfiles actuales. Esta noción de transversalidad se puede formalizar según el modelo de Jensenius [12, 13], que propone varios niveles de disciplinariedad de manera visual, tal y como se muestra en la figura siguiente.
Figura 2. Modelo de disciplinariedades de Jensenius y Stember
Cada uno de los elementos del modelo de Jensenius y Stember [12, 13] de la Figura 2 se puede definir tal y como se describe a continuación:
- Intradisciplinar: personas trabajando dentro de una misma disciplina.
- Multidisciplinar: personas de distintas disciplinas que colaboran cada una con sus conocimientos y sus métodos.
- Crosdisciplinar: visualización de una disciplina desde la perspectiva de otra.
- Interdisciplinar: integración de conocimientos y de métodos de distintas disciplinas realizando una síntesis de varios enfoques.
- Transdisciplinar: creación de una unidad de marcos intelectuales más allá de las perspectivas disciplinarias.
Teniendo en cuenta esta visión de las disciplinariedades, el freno en la adopción tecnológica se puede analizar siguiendo el modelo de Anthony [14], que plantea los tres niveles clásicos de la gestión de las organizaciones desde el punto de vista de la toma de decisiones estratégico, táctico y operacional, que se pueden asociar al plazo temporal (largo, medio y corto) y también a los perfiles profesionales (directivos, gestores, técnicos) que los ejecutan.
Por un lado, en el plano estratégico vemos que hay grandes dificultades para tener una visión clara y liderazgo, puesto que se debe tener en cuenta que la dirección de la empresa es clave para impulsar la adopción de estas tecnologías en los diferentes ámbitos, seleccionando las palancas a utilizar y definiendo qué nivel de intensidad debe aplicarse a cada palanca. En este sentido, la falta de conocimiento del potencial y de la aplicabilidad de las nuevas tecnologías, y todavía más importante, de sus combinaciones, reduce la voluntad de realizar inversiones por que se desconoce cuál es el coste de implantación y el tiempo de retorno de la inversión.
Por otro lado, por lo que respecta al plan táctico, las dificultades se derivan de la estructura organizativa de las empresas, que crean silos que dificultan la colaboración para el desarrollo y la implantación de proyectos n-disciplinares. Según Tett [15], el efecto «silo» surge cuando la naturaleza de los retos a afrontar necesita colaboración entre varias disciplinas, y esto a menudo requiere una voluntad de colaboración entre los distintos departamentos de la empresa. La falta de empatía entre diferentes perfiles profesionales implicados en el proceso de transformación digital puede incluso perjudicar el éxito de las pruebas piloto que deben validar la tecnología. Teniendo en cuenta esto, para solucionarlo habrá que adaptar las estructuras organizativas y ofrecer incentivos para la colaboración con el fin de fomentar la adopción de las tecnologías 4.0.
Finalmente, por lo que se refiere al plano operacional, uno de los problemas es la convergencia de conocimientos y de competencias entre los diferentes perfiles profesionales. Básicamente esto se refiere a los perfiles del ámbito de las operaciones (OT - Operations Technologies) y de las tecnologías de la información y las comunicaciones (IT - Information Technologies). El reto de lograr la denominada convergencia IT/OT fue planteado por Rockwell Automation en 2007 [16], y es uno de los retos más importantes de transversalidad de la Industria 4.0, ya que además de los elementos de conocimiento intervienen aspectos culturales, como por ejemplo la percepción del tiempo o del riesgo, que son diferentes entre ambos colectivos [17]. Para solucionarlo deberá ofrecerse formación específica de cariz transversal para garantizar que los profesionales tienen las competencias para adoptar las tecnologías [18].
El instrumento más importante para hacer efectiva esta convergencia entre los mundos IT y OT es el denominado gemelo digital (digital twin, o DT), aplicable tanto a los productos como a los sistemas de producción, que consiste en un modelo digital con todas las características constructivas del activo en cuestión (denominado digital master, o DM), combinado con un sistema de información a partir de los datos recogidos de la realidad mediante sensórica, o comunicado por el propio activo (denominado digital shadow, o DS). Según el modelo de DT propuesto por Stark [19], los DM y los DS se relacionan mediante algoritmos, como por ejemplo la simulación, la analítica de datos o la inteligencia artificial. El concepto DT incluye la modelización, la simulación y el internet de las cosas, que comprenden la electrónica empotrada, el software y las telecomunicaciones. El DT permite desarrollar productos y soluciones en el mundo digital (virtual) sin los riesgos del mundo físico, aplicando técnicas provenientes del mundo del software basadas en muchas iteraciones de prueba y de error a alta velocidad, y después pasar al mundo físico con el número mínimo de errores potenciales. Para que esto sea posible, los modelos de simulación deben verificarse y validarse convenientemente utilizando modelos basados en la estadística. Además, el DT, debido al potencial de la simulación, permite la transmisión tanto del conocimiento de tipo explícito como de tipo tácito, este último el más difícil de gestionar [20]. Los DT tendrán un gran impacto en el desarrollo de la transversalidad en la medida en que se extienda la interoperabilidad entre ellos, permitiendo su utilización conjunta en soluciones integradas.
Así pues, la transversalidad de los perfiles profesionales afecta a los ámbitos estratégico, táctico y operacional de la empresa y limita la capacidad de adopción de las tecnologías en todos los ámbitos. Por ejemplo, en el caso del mantenimiento predictivo es necesario el despliegue de dispositivos con capacidad de sensorización y de comunicación para recopilar los datos de la máquina en cuestión, pero también hace falta una infraestructura de computación en la nube que permita almacenarlas, y un conjunto de aplicaciones que utilicen algoritmos de inteligencia artificial que los combinen y extraigan el conocimiento que pueda utilizarse para detectar posibles fallos. Además, la integración de este proceso de generación, transporte y procesado de los datos debe hacerse de manera segura, ya que en algunos casos puede tratarse de información sensible para la empresa, y en otros puede dejar una puerta abierta a ciberataques que detengan el proceso productivo. Es fácil ver, pues, como la responsabilidad del despliegue de estas tecnologías recae en diferentes departamentos de la empresa. Siguiendo con el ejemplo anterior, el despliegue de una solución de mantenimiento predictivo requerirá, como mínimo, la intervención de los departamentos de operaciones, mantenimiento y tecnologías de la información y la comunicación. De manera simplificada, podemos decir que los primeros serán los encargados de definir los elementos que es necesario sensorizar, los segundos se encargarán de desplegarlos y de mantenerlos, y los terceros serán los encargados de proporcionar la infraestructura para recibir, almacenar y procesar los datos. A pesar de los beneficios que pueden aportar las tecnologías digitales en el ámbito de la industria, debe tenerse en cuenta que su aplicación también incrementa la complejidad de los sistemas y su incertidumbre. Por ejemplo, a medida que los sistemas industriales están conectados a internet para llevar a cabo la monitorización y el control, crece el riesgo de sufrir un ciberataque.
En los últimos años, el número de iniciativas de impulso a la Industria 4.0 no ha dejado de crecer. En el año 2018, en la Unión Europea había dieciocho iniciativas aprobadas impulsadas por varios gobiernos. Para coordinarlas y empoderarlas está la iniciativa llamada Digitizing European Industry (DEI), con una dotación de 5.000 millones de euros del programa Horizon 2020 [21], vinculada a una de las cinco prioridades más importantes de la Unión, denominada Digital Single Market.
Pero a pesar del interés y del impacto potencial que tiene la adopción de las diferentes tecnologías en el marco de la Industria 4.0, la realidad es que el proceso de adopción de estas tecnologías no sigue el ritmo previsto inicialmente [22], tanto por lo que respecta a la tasa de adopción de la tecnologías como a la profundidad de las transformaciones que implica su adopción. De hecho, según este estudio, solo el 29% de las empresas industriales han empezado a desplegar estas tecnologías en sus procesos (las que podemos considerar innovadoras y seguidoras iniciales), mientras que el 71% restante se divide entre las que han empezado a hacer pruebas piloto (mayoría precoz) y las que no han empezado ninguna actividad en esta dirección (mayoría tardía y atrasadas). También se constata que las pyme presentan, en general, niveles de adopción inferiores a los de las grandes empresas [23], y que los niveles de adopción varían según los países [24]. Esto nos sitúa aún en el primer tramo de la curva-S, de manera que los tejidos industriales todavía no han entrado en el tramo de fuerte aceleración de manera generalizada.
A la vista de estas dificultades para integrar las tecnologías de la Industria 4.0, en 2017 la VDMA (asociación industrial de ingenieros mecánicos de Alemania) publicó un documento de trabajo [25] en el que propone un modelo para facilitar la adopción de las tecnologías. Este modelo consta de cinco fases: preparación, análisis, creación, evaluación e introducción. En la fase de preparación se crean equipos de trabajo que tengan conocimientos del mercado y de los procesos productivos de la empresa. En la fase de análisis se identifican las competencias existentes dentro de la empresa respecto a las tecnologías de la Industria 4.0 y se comparan con la competencia. En la fase creativa se generan ideas que pueden resultar en proyectos que permitan la mejora de los procesos y de los productos de la empresa. En la fase de evaluación se seleccionan los proyectos que se considera relevantes y se construye un equipo encargado de llevar a cabo un despliegue piloto para comprobar la viabilidad técnica y económica del proyecto. Finalmente, en la fase de implementación los proyectos que han demostrado la viabilidad técnica y económica pasan a desplegarse.
Así pues, siguiendo las recomendaciones de adopción de la tecnología, las empresas más innovadoras de todo el mundo han empezado a trazar sus planes de adopción según su sector y en función de sus necesidades técnicas y de su capacidad de inversión. Principalmente se han definido y llevado a cabo pruebas piloto para validar el interés de cada tecnología según el ámbito de aplicación y el retorno de la inversión esperado, así como para entender cómo estas tecnologías pueden escalar el volumen requerido. Además, las empresas también han aprovechado para empezar a formar a sus empleados sobre los aspectos técnicos y los fundamentos directivos relacionados con el proceso de transformación digital. Pero según el informe de KPMG de 2018 «A reality check for today’s C-Suite on Industry 4.0» [26], el tiempo de solo experimentación se está acabando, ya que donde ha habido una proliferación de pruebas piloto al final se tiende a ir hacia «silos», que a menudo acaban siendo una sobrecarga porque no aportan claridad en la visión estratégica.
La dificultad en la adopción de las tecnologías digitales no radica en su novedad en sí, ya que, como se ha visto, prácticamente todas ellas existen desde hace años. La cuestión es que muchas de ellas han llegado simultáneamente a un nivel de madurez suficiente que ha abierto escenarios a muchas posibles nuevas combinaciones con potencial transformador. Según Frank Diana [27], se han creado unas condiciones muy favorables para la combinación de tecnologías que él denomina combinatorial scenarios y que pronostican una curva-S con una pendiente muy pronunciada. Si la velocidad de generación de nuevas combinaciones potenciales es mayor que la velocidad de exploración y de evaluación de las mismas, aumenta la dificultad para tener una visión estratégica clara que permita adoptarlas y sacarles partido.
La cuestión de los perfiles profesionales y de la Industria 4.0 se define por una situación de realimentación permanente. Por un lado, según Kagermann [3], la Industria 4.0 transformará radicalmente los perfiles competenciales y profesionales del ámbito industrial. Por otro lado, las organizaciones están demandando perfiles profesionales distintos o nuevos para sacar adelante la transformación digital. Así pues, en esta sección analizamos el impacto laboral, los nuevos perfiles profesionales y las necesidades formativas en el marco de la Industria 4.0.
Los estudios sobre el impacto laboral de la Industria 4.0 se pueden dividir en dos grandes grupos, y en este apartado se presenta una síntesis de resultados cuantitativos de los estudios identificados.
El primer grupo está orientado a identificar y cuantificar los puestos de trabajo que tienen una alta probabilidad de ser automatizados. El trabajo seminal de este primer grupo es el estudio realizado por Frey y Osborne [28], iniciado en 2013 en la Universidad de Oxford y publicado en 2017, en el que se relaciona una lista de 702 puestos de trabajo, y la probabilidad de cada uno de ser automatizado. Otros estudios a destacar son los publicados por Arntz, Gregory y Zierahn (OCDE) en 2016 [29], por la consultoría McKinsey en 2017 [30], y el estudio de Morrón (CaixaBank) en 2016 [31]. A pesar de que estos estudios dan resultados distintos según la zona geográfica, en general hay el consenso de que cerca de un 40% de los puestos de trabajo tienen un 70% de probabilidades de ser automatizados en un horizonte temporal de alrededor de una década.
El segundo grupo de estudios está orientado a identificar los posibles efectos de creación y de destrucción de puestos de trabajo, detectando tendencias en cuanto a nuevos perfiles demandados. Los cinco estudios más remarcables son los dos de ámbito global publicados por el World Economic Forum en 2016 [21] (posteriormente actualizado en la versión de 2018 [32]) y por el estudio de McKinsey en 2017 [33]; los dos de ámbito alemán publicados por Vogler-Ludwig, Düll y Kriechel en 2016 [34]; y el de Boston Consulting Group en 2015 [2]. Por último, en el ámbito catalán cabe destacar el estudio realizado por Hernández-Gascón en 2018 [35]. De manera resumida, los estudios de impacto de la Industria 4.0 realizados en el ámbito global del World Economic Forum y de McKinsey coinciden en predecir una destrucción de ocupación en términos globales. En el primero se vaticina una destrucción de siete millones de puestos de trabajo y una creación de dos millones de nuevos puestos, dando una destrucción neta de cinco millones, con horizonte 2020. En el segundo estudio se pronostica una destrucción global del 15% de puestos de trabajo con horizonte 2030, pero a pesar de que se destaca que se crearán nuevos puestos en diferentes áreas (ingeniería, ciencia, salud, informática, directivas, docencia y creativas), no se cuantifica el volumen global de los nuevos puestos creados. En cambio, según los estudios de impacto realizados en el ámbito alemán y catalán, la Industria 4.0 creará más puestos de trabajo de los que se destruirán. El estudio de Boston Consulting Group pronostica la creación de 210.000 puestos de trabajo cualificados con horizonte 2025, y el de Vogler-Ludwig estima la creación de 263.000 puestos de trabajo con horizonte 2030 como consecuencia de la Industria 4.0. En el caso catalán, el estudio de Hernández-Gascón vaticina la creación de 13.000 puestos de trabajo cualificados con horizonte 2030.
Además del debate sobre la creación y la destrucción de puestos de trabajo resultantes del proceso de transformación digital, otro de los aspectos clave en el proceso de adopción de las tecnologías de la Industria 4.0 es la emergencia de nuevos perfiles profesionales. En este sentido, a principios de esta década apareció la figura del CDO (Chief Digital Officer), identificado por la consultoría Gartner [36] como una nueva figura directiva del denominado C-Suite [37], y que tiene el rol de formular el plan de transformación digital de la empresa para que el resto del equipo directivo lo adopte y se lleve a cabo en los distintos niveles operativos. Así pues, según el modelo de Jensenius y Stember, el CDO asume un modelo de transformación digital de la empresa basado en una visión solo multidisciplinar, donde el resto del equipo directivo pertenece a diferentes disciplinas y no comparte conocimientos ni métodos para llevarlo a cabo.
Si bien esta aproximación resultó atractiva inicialmente puesto que minimizaba el impacto del proceso de transformación sobre el resto de departamentos, el informe de PwC de 2019 [38] realizado sobre 2.500 empresas demuestra el declive de la figura del CDO, tal y como aparece en la Figura 3. Como se puede ver, de 2013 a 2016 se pasó de 50 a 150 contrataciones de este perfil, mientras que de 2016 a 2018 se pasó de 150 a 50 contrataciones. Este crecimiento y declive de la figura del CDO es debido a que el proceso de transformación digital es más profundo y requiere un nivel de conocimiento y de implicación de todas las partes que atraviesan de manera inevitable los diversos «silos» que pueda haber en la organización [39].
Figura 3. Contrataciones anuales de CDO. Fuente: Estudio PwC [38]
Por lo tanto, la naturaleza del problema de la digitalización de la industria es de transversalidad, tanto en el plano estratégico como operacional, y afecta al conjunto de la organización. En este sentido, el informe de 2015 de la asociación de ingenieros alemana VDI y de la asociación de ingenieros americana ASME [11] advierte claramente que los perfiles profesionales dominantes de la Industria 4.0 serán interdisciplinares en detrimento de los solo multidisciplinares3.
A la vista de las necesidades de perfiles interdisciplinares, en 2019 la Fundació IMPULS ha publicado un trabajo de investigación que tiene como objetivo definir los perfiles profesionales de la Industria 4.0 [40]. Para ello, los investigadores han realizado un total de 224 cuestionarios a los principales grupos de interés (a estudiantes y profesores universitarios, así como a líderes técnicos y directores generales de empresas) con el objetivo de comprender las competencias técnicas e interpersonales necesarias para desarrollar proyectos en el contexto de la Industria 4.0.
El resumen de los resultados está publicado en el informe de 2019 «Ingenieros para la Industria 4.0» [4], y como ejemplo de los resultados obtenidos, en el estudio hay una pregunta que se centra en las competencias complementarias del dominio de las TIC (tecnologías de la información y la comunicación) que serían necesarias para los ingenieros industriales en el contexto de la Industria 4.0. Los resultados muestran que las habilidades técnicas relacionadas con la seguridad de la información y las comunicaciones (58%), la recopilación, el almacenamiento y la preparación de datos (58%), y los algoritmos (49%) son habilidades consideradas muy útiles o imprescindibles para los futuros ingenieros industriales.
Si bien este estudio se centra en Alemania, y por lo tanto no es representativo de la realidad industrial de nuestro país, es indicativo de que debe replantearse la formación técnica, tanto en el plano universitario como de ciclos formativos, teniendo en cuenta las nuevas competencias técnicas y las competencias interpersonales que requiere la Industria 4.0, y que se han descrito anteriormente. En caso de no hacerlo, o de hacerlo solo parcialmente, corremos el riesgo de frenar el ritmo de adopción de estas tecnologías en nuestro tejido industrial y poner en peligro la continuidad de las empresas de nuestro país.
En la misma línea de las competencias requeridas por la Industria 4.0, pero centrado en el sector del mueble y la madera en Cataluña, la fundación CENFIM (Centre de Difusió Tecnològica Fusta i Moble de Catalunya) ha publicado en 2019 un estudio sobre el impacto de la transformación digital en la industria del mueble de madera. Este informe se ha realizado en el marco del proyecto europeo DIGIT-FUR [41] y presenta un mapeo del impacto sobre cada una de las tareas de los perfiles profesionales actuales, tanto de carácter técnico como comercial, de las nueve tecnologías transformadoras de la Industria 4.0 propuestas en el modelo de Boston Consulting Group, y también con las veintiséis palancas de la Industria 4.0 propuestas en el modelo de McKinsey.
Fruto del trabajo realizado, el estudio concluye que de las siete competencias esenciales identificadas para el trabajador de planta del sector del mueble y la madera, solo uno queda igual, cuatro se modifican y dos desaparecen. En cambio, para los directores comerciales, de las nueve competencias identificadas, dos quedan iguales y siete se modifican. A la vista de esta proyección, el estudio hace recomendaciones en el ámbito de la formación, tanto en los ámbitos universitarios como en el de la formación profesional, y prevé la aparición de nuevos perfiles profesionales, en particular el de directivo de transformación digital (en inglés, Digital Transformation Manager).
Como continuación del proyecto DIGIT-FUR, en 2019 también se ha puesto en marcha el proyecto europeo DITRAMA (www.ditrama.eu), que tiene como finalidad identificar y definir las habilidades y las competencias de este nuevo perfil. El proyecto apenas ha empezado, pero en su desarrollo ya se están tratando conceptos como el gemelo digital (del inglés, digital twin), la servitización y las plataformas colaborativas, la innovación abierta y la economía circular, entre otros. Además, según el trabajo llevado a cabo hasta el momento, el perfil del DTM puede encuadrarse en cada dominio del C-Suite, de manera que la transformación digital de la organización se puede hacer simultáneamente desde cada área mediante la colaboración transversal de los diferentes DTM, y no desde una única área comandada por un CDO, lo que se corresponde con la necesidad de transversalidad.
En esta sección se analiza la figura de los expertos y de los grupos de trabajo en la Industria 4.0, que está dando lugar a la aparición de herramientas de diagnosis dirigidas a las empresas y a las organizaciones, con el fin de medir y evaluar su adopción. Finalmente, se analiza la relación entre las necesidades formativas y los diversos tipos de perfiles profesionales considerados.
La figura del experto ha resurgido con fuerza en el marco de la Industria 4.0 como resultado de la construcción de un cuerpo de conocimiento que combina las diferentes disciplinas de la ingeniería para hacer frente al proceso de transformación digital de los productos y de los procesos. Además de participar como actor principal del proceso de transformación digital de empresas del sector industrial, los expertos también participan como miembros de los diferentes grupos de trabajo que se han creado alrededor de la Industria 4.0.
Según el informe de KPMG [9], en 2016 estaban identificados varios grupos de trabajo de expertos orientados al desarrollo de la Industria 4.0. El primero de ellos fue impulsado por el gobierno alemán para preparar la iniciativa Industrie 4.0, presentada en 2013 a la canciller Angela Merkel en el contexto de la Feria de Hannover. Desde entonces, las asociaciones empresariales alemanas como la VDMA (asociación de empresas de ingeniería mecánica), la ZVEI (asociación de empresas fabricantes de equipos eléctricos y electrónicos) o la Bitkom (asociación de empresas de informática y telecomunicaciones) han continuado las tareas del grupo de trabajo inicial [9], dando lugar a la llamada Industrie Plattform 4.0 que además incluye a la administración pública, sindicatos, empresas y asociaciones profesionales como la VDI (equivalente en la ingeniería industrial) o la VDE (equivalente a las ingenierías informáticas y telecomunicaciones). El segundo grupo de expertos, es Industrial Internet Consortium (IIC) [9], una entidad privada con sede en los Estados Unidos que dispone de una estructura de grupos de trabajo de ámbito global con una potencia similar a la Plattform alemana. Entre otros, el IIC se encarga de organizar el IOT Solutions World Congress, que se celebra anualmente en Barcelona durante el mes de octubre.
Tanto la Plattform como el IIC impulsan la formalización de la Industria 4.0, mediante las denominadas arquitecturas de referencia que definen los componentes y su integración de manera agnóstica respecto a las tecnologías. Por un lado, tenemos la Reference Architecture Model Industry 4.0 (RAMI 4.0) [42], recogida como estándar IEC/PAS 60833, y por otro lado, tenemos la Industrial Internet Reference Architecture (IIRA) [43]. Además, ambas organizaciones han creado un grupo de trabajo transversal para definir un mapeo entre las dos arquitecturas, facilitando que puedan utilizarse complementariamente. Teniendo en cuenta que por razones históricas RAMI 4.0 tiene raíces en el mundo OT (Operations Technologies) e IIRA tiene raíces en el mundo IT (Information Technologies), esta unificación facilitará la convergencia IT/OT, que es aspecto clave en la adopción de la Industria 4.0.
Finalmente, en el ámbito catalán debe destacarse que en 2014 se constituyó la Comissió Indústria 4.0, formada inicialmente por las asociaciones y colegios profesionales de los ingenieros industriales, informáticos y de telecomunicaciones, a la que se añadieron los ingenieros agrónomos, los ingenieros de caminos y los ingenieros químicos y de nuevos materiales [44]. Esta comisión cuenta con los grupos de trabajo de robótica, IoT y sistemas empotrados, fabricación aditiva, intralogística, software e integración, agricultura, inteligencia artificial y de nuevos materiales. En este período, los grupos de trabajo de la comisión han publicado diversos documentos vinculados a la Industria 4.0, como un status report [44], una guía de adopción para pymes y un documento base para crear una herramienta de diagnóstico.
Los marcos de referencia RAMI 4.0 e IIRA combinados con los modelos de adopción de las tecnologías permiten que la comunidad de expertos y los grupos de trabajo puedan construir un discurso transversal consistente de la Industria 4.0. Pero solo con marcos de referencia no es suficiente para avanzar en el proceso de transformación digital, debido a que son conceptuales y agnósticos respecto a las tecnologías específicas. Así pues, para llegar a la concreción también han surgido las herramientas de diagnosis y las hojas de ruta. Por un lado, las herramientas de diagnosis se definen como un cuestionario sobre la posición de las organizaciones respecto a un conjunto de palancas y a un modelo conceptual que traduce las respuestas en resultados cuantificables. Por otro lado, las hojas de ruta se definen como una sucesión en el tiempo de niveles de intensidad en la aplicación de un conjunto de palancas previamente seleccionadas y priorizadas según las necesidades de cada empresa.
La aplicación de las hojas de ruta y de las herramientas de diagnosis favorecen la adopción de la Industria 4.0, de manera que en los últimos tres años han aparecido varias herramientas de diagnosis como la de la Acatech [45], la HADA del Ministerio de Industria, Comercio y Turismo [46] o la de PwC [47]. En general, sin embargo, estas herramientas son poco transparentes, lo que ha provocado que la comunidad de expertos no las haya podido utilizar, comparar, combinar y hacer evolucionar abiertamente. A su vez, esto ha dificultado enormemente la adopción de métodos de definición y la puesta en práctica de hojas de ruta mínimamente consensuadas.
Así pues, con el objetivo de facilitar el acceso a estas herramientas de diagnosis, la Comissió Indústria 4.0, de ingenieros de Cataluña, presentó en octubre de 2018 una propuesta abierta (www.comissioindustria40.cat/documents) que ha dado lugar a un cuestionario en línea. Este cuestionario se puede utilizar como un instrumento básico para realizar una primera reflexión sobre el grado de adopción respecto a varias palancas de la Industria 4.0. Además, gracias a que sigue un modelo abierto, este cuestionario también ha servido de base para otras herramientas de diagnosis, como es el caso de la Eina de nivell de maduresa digital de la iniciativa Terrassa 4.0 (www.terrassa.cat/eina-nivell-de-maduresa-digital).
A la vista de los modelos y de los resultados de los diferentes estudios que se han presentado en este artículo, en la Tabla 1 proponemos un mapeo4 entre los perfiles profesionales (técnicos, gestores, directivos, expertos y estudiantes) y los niveles de la empresa (estratégico, táctico y operacional). El objetivo de esta tabla es mostrar cuáles deben ser las líneas de actuación prioritarias en cada ámbito, y que debe permitir impulsar la adopción de la Industria 4.0, y superar los frenos de falta de visión estratégica clara y la carencia de perfiles profesionales con la transversalidad adecuada, acelerando así la llegada del segundo tramo de la curva-S de manera generalizada.
Tabla 1. Relación de necesidades formativas y tipos de perfiles profesionales
Nivel estratégico | Nivel táctico | Nivel operacional | Ámbito | |
Técnicos | Es necesario que adquieran conocimientos transversales para poder combinar las diferentes tecnologías. | Ejecutan las hojas de ruta. Actúan transversalmente con otros técnicos. |
Organitzación | |
Gestores | Deben luchar contra los «silos informativos y de conocimieto» siguiendo las directrices de los directivos. | Definen hojas de ruta. Utilizan herramientas de diagnosis y de seguimiento. |
Supervisan y apoyan la ejecución operacional de las hojas de ruta Actúan transversalmente con otros gestores. |
|
Directivos | Deben luchar contra los «silos organizativos y de mentalidad». Introducen transversalidad digital en el C-Suite. |
Interpretan los resultados de las herramientas de diagnosis y de seguimiento. Crean las condiciones para que se puedan definir hojas de ruta. |
Apoyan en el ámbito táctico la ejecución de las hojas de ruta. | |
Expertos | Deben luchar para aumentar su transversalidad más allá de su diligencia en palancas específicas. Asesoran a organismos públicos en programas de desarrollo y a organizaciones. |
Desarrollan metodologías para definir y seguir hojas de ruta. Desarrollan herramientas de diagnosis. |
Participan en publicaciones. Realizan tareas docentes y participan en acontecimientos. Promueven transversalidad digital a todos niveles (C-Suite, gestores y técnicos y estudiantes). |
Tejido industrial |
Estudiantes | Hay que actualizar la base común de las ingenierías basada en álgebra, cálculo, física, química y dibujo técnico a los nuevos tiempos. | Debido a la falta de estos perfiles en la actualidad, los profesio-nales de la industria se están formando en programas de posgrado. | Frealizan prácticas o los trabajos de fin de estudios en empresas. |
Resumidamente, podemos concluir que los perfiles del tipo estudiante requieren reorientación en cuanto a conocimientos transversales (salvo los programas de posgrado específicos), el perfil directivo debe adaptarse incorporando transversalidad estratégica, el perfil de gestor de transformación digital es emergente y sus funciones están todavía por definir, los perfiles técnicos (tanto de ingenieros como de formación profesional) serán muy demandados pero con nuevos elementos de transversalidad y, finalmente, el perfil de experto es emergente pero como colectivo todavía actúa con poca transversalidad.
Como hemos visto, la relación causa efecto entre Industria 4.0 y los perfiles profesionales es bidireccional, y da lugar a una situación de realimentación mutua. Por un lado, la Industria 4.0 tendrá impacto en la mayoría de perfiles profesionales y modificará la mayoría de sus competencias, añadiendo nuevas y eliminando algunas de las existentes. Además, también se crearán nuevos perfiles profesionales de manera integral, como por ejemplo el Digital Transformation Manager. Por otro lado, los perfiles profesionales impactarán sobre la Industria 4.0, ya que el tejido industrial que disponga de ella podrá transformarse antes y con garantías de éxito, lo que le permitirá continuar siendo competitivo en un mundo global.
No obstante, según los estudios realizados, todavía no se ha llegado de manera generalizada al segundo tramo de la curva-S, en la que se prevé la entrada en una fase de fuerte aceleración, afectando a las pequeñas y medianas empresas, que representan el porcentaje más alto del volumen total de empresas. Varios estudios coinciden en que los frenos más importantes para la entrada en esta fase son la falta de visión estratégica clara y la carencia de perfiles profesionales transversales adecuados. Teniendo en cuenta esto, uno de los grandes retos asociados a la transformación en el ámbito de la industria es precisamente la falta de perfiles profesionales que comprendan la tecnología y a la vez sean capaces de entender su aplicación en el ámbito concreto.
Como resultado del análisis realizado, se han identificado los siguientes desajustes entre los requisitos de la Industria 4.0 y los perfiles profesionales que existen actualmente:
- Carencia de técnicos y gestores con los conocimientos digitales y las competencias transversales requeridas.
- Carencia de fundamentos conceptuales digitales de aplicación transversal en directivos que deben liderar una transformación digital con una visión estratégica clara.
- Carencia de herramientas disponibles creadas o apoyadas por los expertos que permitan diseñar y ejecutar hojas de ruta de adopción de la Industria 4.0.
- Carencia de actualización en la base común de los planes de estudio de las ingenierías que permita tener profesionales con los conocimientos y las competencias requeridos.
Además, en este artículo se han identificado las causas que relacionan la dificultad en la adopción de la Industria 4.0 con la cuestión de los perfiles profesionales, sobre base de la distinción de cinco perfiles profesionales clave: directivo, gestor, técnico, estudiante (formación reglada y formación continua) y experto. De cada perfil se han identificado las tareas que tienen incidencia en los dos frenos más importantes, y a partir de ellas se han identificado los desfases en cuanto a perfiles profesionales que ocasionan este freno, llegando a las siguientes conclusiones:
- La falta de herramientas de diagnosis transparentes y compartidas es una limitación en la transversalidad de los expertos, y es crítica puesto que frena que los directivos puedan tener una visión estratégica clara, condenándolos a seguir avanzando en la adopción de las tecnologías de la Industria ٤.٠ solo con pruebas piloto internas.
- La formación continuada, tanto de posgrado como de capacitación profesional, es la vía más importante para modificar los perfiles profesionales existentes en la actualidad, y para crear los nuevos perfiles requeridos mientras no se actualicen los planes de estudios de las formaciones regladas.
- Los gemelos digitales (digital twins) se perfilan como una herramienta clave para desarrollar transversalidad en sentido amplio, tanto en los ámbitos formativos como en los planos estratégico, táctico y operacional de las organizaciones y del propio tejido industrial, a la espera de que se generalice la interoperabilidad entre ellos.
[1] WESTERMAN, G.; CALM JANE, C; BONNET, D., et al. (2011). «Digital transformation: A road-map for billion-dollar organizations». MIT Center for Digital Business y Capgemini Consulting [en línea].
[2] GERBERT, P.; LORENZ, M. RÜßMANN, M., et al. (2015). «Man and Machine in Industry 4.0. How Will Technology Transform the Industrial Workforce Through 2025?». The Boston Consulting Group [en línea].
[3] KAGERMANN, H.; WAHLSTER, W.; HELBIG, J. (2013). «Recommendations for implementing the strategic initiative INDUSTRIE 4.0: Final report of the Industrie 4.0 Working Group». Acatech [en línea].
[4] INDUSTRIE 4.0 FORUM (2016). «Industrie 4.0 in practice: Solutions for industrial applications». VDMA Industrie 4.0 newsletter. VDMA [en línea].
[5] ROGERS, E. M. (1983). Diffusion of Innovations (3.ª ed.). The Free Press (1983). Nueva York.
[6] MCKINSEY & COMPANY (٢٠١٥). «Industry ٤.٠: How to navigate digitization of the manufacturing sector». McKinsey Digital [en línea].http://www.forschungsnetzwerk.at/downloadpub/mck_industry_40_report.pdf
[7] DICKHOUT, R. (1997). «All I ever needed to know about change management I learned at engineering school». McKinsey Quarterly [en línea].https://www.mckinsey.com/business-functions/organization/our-insights/all-i-ever-needed-to-know-about-change-management-i-learned-at-engineering-school
[8] PwC (2018). «Global Digital Operations 2018 Survey». Strategy & Global [en línea].https://www.strategyand.pwc.com/industry4-0
[9] HEINITZ, H. V.; BREMICKER, M. (2016). «The Factory of the Future. Industry 4.0 - The challenges of tomorrow». KPMG [en línea].https://assets.kpmg/content/dam/kpmg/pdf/2016/05/factory-future-industry-4.0.pdf
[10] KROLL, H., et al. «An analysis of drivers, barriers and readiness factors of EU companies for adopting advanced manufacturing products and technologies». Comisión Europea.
[11] GEHRKE, L., et al. (2015). «A Discussion of Qualifications and Skills in the Factory of the Future: A German and American Perspective». White paper. VDI/ASME [en línea].https://www.vdi.de/ueber-uns/presse/publikationen/details?tx_vdipublications_publicationdetails%5Bpublication%5D=117
[12] JENSENIUS, A. R. (2012). «Disciplinarities: intra, cross, multi, inter, trans» [en línea].http://www.arj.no/2012/03/12/disciplinarities-2
[13] STEMBER, M. (1991). «Advancing the social sciences through the interdisciplinary enterprise». The Social Science Journal. Vol. 28, n.o 1, págs. 1-14.
https://doi.org/10.1016/0362-3319(91)90040-B
[14] ANTHONY, G; SCOTT MORTON, M. (1971). «A framework for management information systems». Sloan Management Review. N.o 13, págs. 55-70.
[15] TETT, G. (2015). «The Silo Effect». The Guardian [en línea].https://www.theguardian.com/books/2015/oct/17/the-silo-effect-why-putting-everything-in-its-place-isnt-such-a-bright-idea-gillian-tett-review
[16] CONTROL ENGINEERING STAFF (2007). «Benefits suggested with convergence of IT, controls». Control Engineering Daily News [en línea].https://www.controleng.com/articles/benefits-suggested-with-convergence-of-it-controls
[17] STOUFFER, K; LIGHTMAN, S.; PILLITTERI, V., et al. (2015). «Guide to Industrial Control Systems (ICS) Security». NIST Special Publication. N.o 800-82. National Institute of Standards and Technology [en línea].
https://csrc.nist.gov/publications/detail/sp/800-82/rev-2/final
https://doi.org/10.6028/NIST.SP.800-82r2
[18] HARP, D. R.; GREGORY-BROWN, B. (2013). «IT/OT Convergence. Bridging the Divide». https://ics.sans.org/media/IT-OT-Convergence-NexDefense-Whitepaper.pdf
[19] STARK, R., et al. (2017). «Innovations in digital modelling for next generation manufacturing system design». CIRP Annals. Vol. 66, n.o 1, págs. 169-172.
https://doi.org/10.1016/j.cirp.2017.04.045
[20] NONAKA, I. (1994). «A dynamic theory of organizational knowledge creation». Organization Science. Vol. 5, n.o 1, págs. 14-37.
https://doi.org/10.1287/orsc.5.1.14
[21] WORLD ECONOMIC FORUM (2016). «The Future of Jobs. Employment, Skills and Workforce Strategy for the Fourth Industrial Revolution». Global Challenge Insight Report [en línea].http://www3.weforum.org/docs/WEF_Future_of_Jobs.pdf
[22] WORLD ECONOMIC FORUM (2018). «The Next Economic Growth Engine: Scaling Fourth Industrial Revolution Technologies in Production». White paper [en línea]. http://www3.weforum.org/docs/WEF_Technology_and_Innovation_The_Next_Economic_Growth_Engine.pdf
[23] CÁMARA DE COMERCIO, INDUSTRIA, SERVICIOS Y NAVEGACIÓN DE ESPAÑA (2018). «España Empresa Digital - La digitalización como palanca de competitividad de la PYME». TIC Cámaras. Unión Europea [en línea].https://empresadigital.camara.es/sites/empresadigital.camara.es/files/generica/informe_espana_empresa_digital_0.pdf
[24] AULBUR, W.; ARVIND, C. J.; BIGGHE, R. (2016). «Skill Development for Industry 4.0». Roland Berger [en línea]. http://www.globalskillsummit.com/whitepaper-summary.pdf
[25] ANDERL, R.; FLEISCHER, J. (2016). «Guideline Industrie 4.0: Guiding principles for the implementation of Industrie 4.0 in small and medium sized businesses». VDMA [en línea]. https://industrie40.vdma.org/documents/4214230/0/Guideline%20Industrie%204.0.pdf/70abd403-cb04-418a-b20f-76d6d3490c05
[26] HARRIS, P.; HENDRICKS, M.; LOGAN, E. A.; JURAS, P. (2018). «A reality check for today’s C-suite on Industry 4.0 The time for experimentation is ending». KPMG [en línea].
[27] DIANA, F. (2015). «Disruptive Power Lies at the Intersections». Frank Diana’s Blog [en línea].https://frankdiana.net/2015/05/18/disruptive-power-lies-at-the-intersections
[28] FREY, C. B.; OSBORNE M. A. (2017). «The future of employment: How susceptible are jobs to computerisation?». Technological Forecasting and Social Change. Vol. 114, n.o C, págs. 254-280 [en línea].
https://doi.org/10.1016/j.techfore.2016.08.019
[29] ARNTZ, M.; GREGORY, T.; ZIERAHN, U. (2016). «The Risk of Automation for Jobs in OECD Countries: A Comparative Analysis». OECD Social, Employment and Migration Working Papers. N.o 189. OECD Publishing. Paris [en línea]. https://doi.org/10.1787/5jlz9h56dvq7-en
[30] MANYIKA, J.; CHUI, M.; MIREMADI, M., et al. (2017). «A Future that Works: Automation, Employment and Productivity». McKinsey & Company [en línea].
[31] MORRON, A. (2016). «Llegará la Cuarta Revolución Industrial en España?». Las nuevas tecnologías y el mercado de trabajo. CaixaBank Research.
https://www.caixabankresearch.com/ca/llegara-la-cuarta-revolucion-industrial-a-espana-d3
[32] WORLD ECONOMIC FORUM (2018). «The Future of Jobs Report 2018».https://www.weforum.org/reports/the-future-of-jobs-report-2018
[33] MANYIKA, J.; LUND, S.; CHUI, M., et al. (2017). «Jobs Lost, Jobs Gained: Workforce Transitions in a time of Automation. McKinsey & Company.
[34] VOGLER-LUDWIG, K.; DÜLL, N.; KRIECHEL, B. (2016). «The German labour market 2030. Economy and labour market in the digital age – Forecast 2016». ResearchGate.
[35] FONTRODONA, J.; MORRON, A.; CASTANY, L. (2018). «L’impacte laboral de la Indústria 4.0 a Catalunya». Papers de l’Observatori de la Indústria. N.o 3. Departament d’Empresa i Coneixement de la Generalitat de Catalunya [en línea]. https://www.accio.gencat.cat/web/.content/bancconeixement/documents/altres_publicacions/03_papers_observatori_industria_40.pdf
[36] COONEY, M. (2012). «Gartner: Do you have a Chief Digital Officer? You’re gonna need one. Gartner. Network World [en línea].
[37] HARRY, A. (2017) «C-Level Executives Mailing List: CEO, CFO, COO, CMO, CTO, CIO, CAO, CXO, CBO, CDO, CISO, CHRO, CSO, CLO, CPO and more...». Medium Corporation [en línea].
[38] PÉLADEAU, P.; ACKER, O. (2019) «Have we reached “peak” chief digital officer?». Tech & Innovation [en línea].
https://www.strategyand.pwc.com/cdo
[39] GREENBAUM, K. (2019). «How Five C-Suite Roles Are Being Reshaped By Business 4.0». Forbes [en línea].
[40] IMPULS (2019). «Engineers for Industrie 4.0». VDMA [en línea].https://bildung.vdma.org/documents/14969637/30466795/IMPULS%2520compact_english.pdf/fed4ab19-d5be-5c35-d54b-6fb12ae0d280
[41] RUMIGNANI, M.; RODRIGO, J.; SOLANA, J. (2019). «Digit-FUr. Impactos de la transformación digital en la industria del mueble de madera». DIGIT-FUR [en línea].
[42] ADOLPHS, P.; EPPLE, U. (2015). «GMA Status Report: Reference Architecture Model Industrie 4.0 (RAMI 4.0)». VDI/VDE/ZVEY [en línea].
[43] LIN, S-W.; MILLER, B.; DURAND, J., et al. (2019) «The Industrial Internet of Things. Volume G1: Reference Architecture». Industrial Internet Consortium [en línea].https://www.iiconsortium.org/IIRA.htm.
[44] COMISSIÓ INDÚSTRIA 4.0 (2017). «Indústria 4.0». Comissió Industria 4.0 de ingenieros de Cataluña [en línea].https://www.comissioindustria40.cat/documents.
[45] SCHUH, G.; ANDERL, R.; GAUSEMEIER, J., et al. (ed.) (2017). «Industrie 4.0 Maturity Index». Acatech [en línea].
https://www.acatech.de/wp-content/uploads/2018/03/acatech_STUDIE_Maturity_Index_eng_WEB.pdf
[46] MINISTERIO DE INDUSTRIA, COMERCIO Y TURISMO. HADA - Herramienta de Autodiagnóstico Digital Avanzada. Ministerio de Industria, Comercio y Turismo [en línea].
https://hada.industriaconectada40.gob.es/hada/register
[47] PWC. «Industry 4.0 - Enabling Digital Operations. Self Assessment» [en línea].
https://i40-self-assessment.pwc.de/i40/landing
- En inglés: innovators, early adopters, early majority, late majority y laggards.
- La noción de palanca aplicada a la gestión tiene su origen en 1997, cuando Dickhout [7] planteó la analogía con una palanca mecánica que se puede situar en una posición a voluntad y que permite controlar un sistema según las necesidades de cada momento.
- Se considera la transdisciplinariedad como una situación no óptima debido al principio económico de coste de oportunidad que, según la teoría de la ventaja comparativa, establece que lo óptimo se obtiene cuando cada actor concentra un determinado nivel de esfuerzo en sus mejores habilidades (skills).
- Es importante destacar que en algunos casos los distintos tipos de perfiles se pueden ejercer simultáneamente. Por ejemplo, el perfil de tipo estudiante se puede ejercer junto con otros de manera permanente bajo un modelo de formación continuada.
PI PALOMÉS, Xavier; TUSET PEIRÓ, Pere. Los nuevos perfiles profesionales en el marco de la Industria 4.0. Oikonomics[en línea]. Noviembre 2019, no. 12, pp. 1-17. ISSN: 2339-9546. DOI: https://doi.org/10.7238/o.n12.1912
ODS
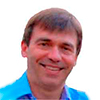
Ingeniero Industrial por la Universitat Politècnica de Catalunya (1988). Actualmente es profesor y codirector del máster en Industria 4.0 de la UPC School y profesor colaborador del máster en Industria 4.0, impartido conjuntamente por los Estudios de Informática, Multimedia y Telecomunicación de la Universitat Oberta de Catalunya y la Escola Superior Politècnica-TecnoCampus, centro adscrito a la Universitat Pompeu Fabra. También es miembro de la Comissió Indústria 4.0 de ingenieros de Cataluña.
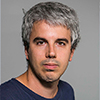
Ingeniero de Telecomunicación por la Universitat Politècnica de Catalunya (2011) y doctor en Tecnologías de la información y las comunicaciones por la Universitat Oberta de Catalunya (2015). Actualmente es profesor y codirector del máster en Industria 4.0, impartido conjuntamente por los Estudios de Informática, Multimedia y Telecomunicación de la Universitat Oberta de Catalunya y la Escola Superior Politècnica-TecnoCampus, centro adscrito a la Universitat Pompeu Fabra.